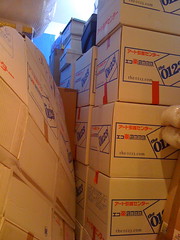
Image by mdid via Flickr
The average consumer doesn’t really care about the details of how a product they ordered gets to them. They just want to make sure it arrives on time and in the perfect condition they expect it to be in. Accomplishing those goals begins with the service at a fulfillment center and with their pick and pack procedures. They need to get it right every time or face the wrath of an angry customer looking for satisfaction.
A successful fulfillment operations needs to be a model in efficiency. Businesses who contract fulfillment centers need to know that they are in good hands. This means having an up to date warehouse management system that can continuously make adjustments in inventory and shipping procedures. It all comes down to volume. The more pick and pack shipments that can go out in a day, the stronger the business becomes by creating a happy customer base. But speed is no excuse for sloppiness.
Pick and pack works best when quality control measures are in place. The first important step is the proper storage of inventory. A recent video made the internet rounds of a vodka fulfillment center in Russia where a hapless forklift driver stumbled into a shelf and created a horrendous domino effect of smashed vodka. The result was a major loss of inventory and disruption in the supply chain. That’s why it is essential that any inventory be placed in a safe and accessible manner. If workers can’t easily access the items they are picking and packing then the day is going to come to a slow crawl.
The next phase for a successful fulfillment operation is to insure that the right items are being packed with the correct corresponding shipping information. This goes back to the properly integrated warehouse management system. UPC and SKU scanners are essential but unless they are programmed and updated with current information they won’t be of any use.
The final phase in a functioning fulfillment center is the actual packing and shipping. Depending on the list of inventory, there can be a myriad of items requiring specific handling care. This can mean quick adjustments in boxes and packing materials. Once again the goal is to keep the supply line moving. If a worker has to stop to search the warehouse more Styrofoam packing peanuts then orders aren’t going to be heading out the door.
The ultimate goal for a fulfillment center is “no returns.” But when returns happen, the cause needs to be examined. If it is a case of a customer changing their mind then the fulfillment center can’t be held accountable. However, if it is an issue of a pick and pack failure then that has to be fixed. Mistakes are unavoidable but when the fulfillment center’s reputation is on the line, they should insure that any break down in pick and pack procedures will be immediately rectified. Maybe if the average customer would spend the day at a fulfillment center they could finally see all the hard work it took to deliver their product, on time and in perfect condition.
