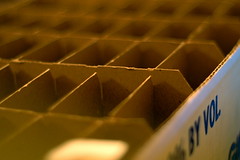
Image by Justin Shearer via Flickr
Whenever someone places an order with an on-line business they can often expect to pay shipping and handling costs. In fact, even before the internet came along, catalog orders were placed over the phone and shipping and handling costs was always part of the expected total price cost of the item. As it was then, today those shipping and handling costs are basically what supports the fulfillment operation and their pick and pack services.
In order to stay competitive a successful fulfillment centers needs to embrace cutting edge technology and state of the art machinery. This comes into play as a company has the potential for expanding their product line. The more products on the shelves, the more chances of varied shipment orders. That puts the pressure on the pick and pack end of fulfillment to step up and get the job done right and one time.
When a fulfillment center can provide service while keeping shipping and handling costs low they can prove to be a valuable asset to a company’s bottom line. One obvious way of keeping costs low is to move out more volume of packages in a given shift. The more merchandise that can move out of the facility equates to the amount of employee hours needed to accomplish that task. That means everyone needs to be working as a team to achieve those goals. Any break down in logistical support can cause a collapse of the line which isn’t going to be good for anyone.
Utilizing cutting edge technology applies directly to inventory restocking and labeling. As shipping orders are processed that information is disseminated into two basic components: the list of the merchandise and the place where the merchandise is headed. That information is entwined in the pick and pack process and should never be separated. Basically, the right piece of inventory has to into the right box with the right address label. That’s fulfillment 101.
Another shipping and handling variation is how fast a person might be excepting their order to arrive at their doorstep. If they have paid extra for priority shipping, which could mean overnight fulfillment, then obviously they are expecting that order the next day. A fulfillment center needs to have a system of “red flag” alerts for those priority shipments to take precedent over the normal flow of pick and pack orders.
An additional variable in shipping and handling costs is when a company offers free shipping. Of course this doesn’t mean that everyone at the fulfillment center is suddenly working for free. But it does mean that the same level of attention to detail has to be maintained through the pick and pack process. A customer might not think they are paying for shipping and handling but chances are those costs have been factored into the price of the item they are buying. The bottom line is that a promise has been made towards expectation of delivery and that promise needs to be kept.
