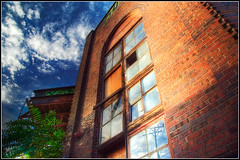
Image by Matthew_Roberts via Flickr
Living in this internet age could really be an extension of our newly developed “microwave society.” Since the invention of the microwave, we’ve grown accustomed to having things delivered to us fast. The internet fits into this paradigm beautifully as information, communication and entertainment are all delivered to our computers in a blink of an eye. The same can be said for shopping on line. The internet has made online shopping one of the most popular ways to shop.
What used to take hours in a trip to the mall can now be accomplished with a few clicks of the mouse and strokes of the keyboard. A specific item that was once only sold from an outlet at one location can now be bought and shipped anywhere in the world. As an order is placed, an inescapable waiting game commences: waiting for order fulfillment. In the microwave society a customer doesn’t want to be kept waiting long.
That fulfillment procedure is indeed a two way street with vital information flowing between order processing and fulfillment. These lines of communication need to be open and constantly updated in order to reach the successful conclusion of putting merchandise into a customer’s hand.
The primary goal of that two way street of information is with maintaining inventory stock levels. The fulfillment center needs to have tracking systems in place that can alert the parent company of any reduction in inventory numbers. And this shouldn’t happen when there are just two items left! There needs to be enough buffer space between a reduction in stock and the ability for that stock to be replenished. That’s going to mean keeping that information going back and forth.
A fulfillment center should be able to implement a system whereby the company can see at any given time where the inventory levels are and if they need restocking. Part of a good communication flow is effective communication. When the pick and pack workers down on the floor log in scans of items being shipped, that information should fly right through the fulfillment center and directly to the company without any stops along the way.
Speaking of the pick and pack staff, they also have to establish open lines of communication with their supervisors and upper management. The best way to know if an operation is running smoothly is by examining it from the ground up. The workers on the warehouse floor will have all kinds of useful information about the best way to access products, how to streamline packaging and basically what can make for a more efficient fulfillment process. Management needs to be open to those ideas and suggestions in order to build up trust and loyalty among the workers. When workers feel respected they take pride in their work. In a fulfillment facility this translates into a high customer satisfaction record when orders are delivered on time and intact. The goal is never to have a traffic jam build up between the customer and fulfillment. As fast as the order was placed, that same level of speed and efficiency needs to be applied up and down the fulfillment chain.
